Are you a manufacturer that has ever been in a position where you were fulfilling an order only to realise that you are out of a necessary component due to a sudden increase in demand? This could mean you need to wait to complete your order, delaying the delivery and resulting in an unhappy customer. If this has ever happened to your business, it may be time to consider Sage warehouse management.
What is safety stock?
Safety stock or buffer stock, as it is commonly referred to, is the level of extra stock that is kept in your warehouse or centre to reduce the risk of running out of inventory. There are many reasons as to why you may need this extra inventory such as uncertainties in supply or demand. Take Covid-19 as an example, there has been added pressure for warehouse inventory management to meet demands in the movement of consumers ordering online.
The purpose of holding such stock is to ensure that once you have run your cycle stock, you are still prepared in case there is a sudden change in demand or even in the supply.
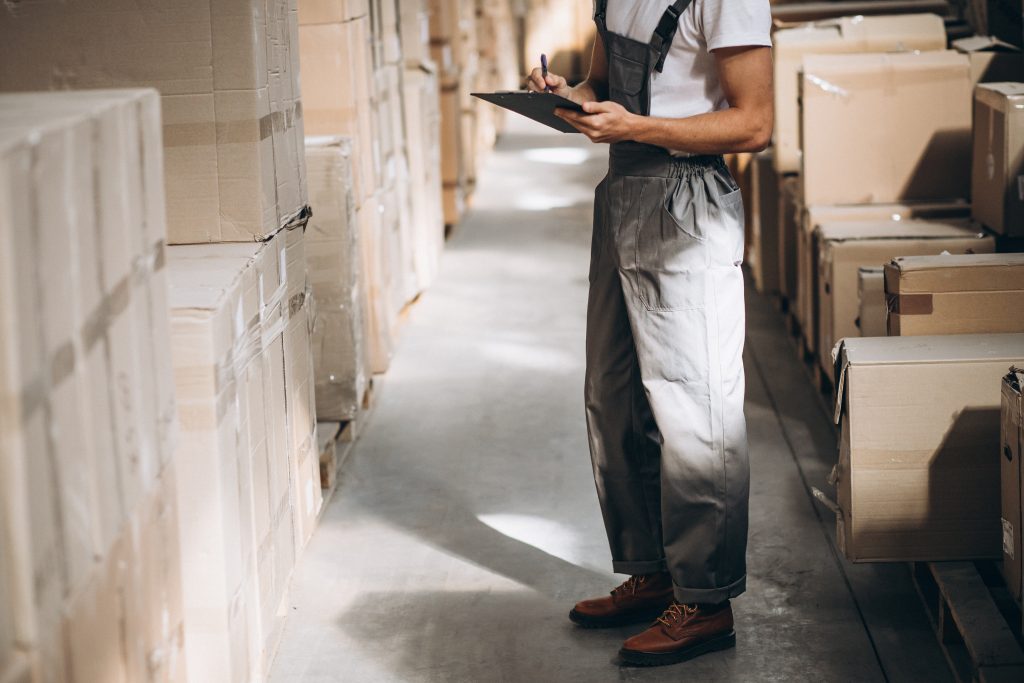
Is keeping safety stock a waste?
When running a warehouse, there are many inventory costs to consider. However, to ensure you meet high levels of customer service and at a high quality of service, accurately calculated inventory and safety stock is a necessity. Like many organisations, you may look at your own demand fluctuations and assume there is not enough consistency to predict future variability. With Sage warehouse management software, you can use a combination of data information to predict accurate levels of stock-based upon historical average demand initially then calculate how much safety stock you may need. This means that safety stock is not a waste, as the levels you order will be accurately forecasted ensuring you don’t waste time and cash.
If you are managing your warehouse manually including data entry and tracking movements of stock, you will find it extremely difficult to forecast inventory trends. As a result, managers can get inventory imbalances that result in excessive inventory costs, impeded cash flow and poor and/or inconsistent service levels all at the same time.
In this blog, we are going to explore some key reasons for carrying safety stock, and how Sage warehouse management can eliminate a lot of waste and errors.
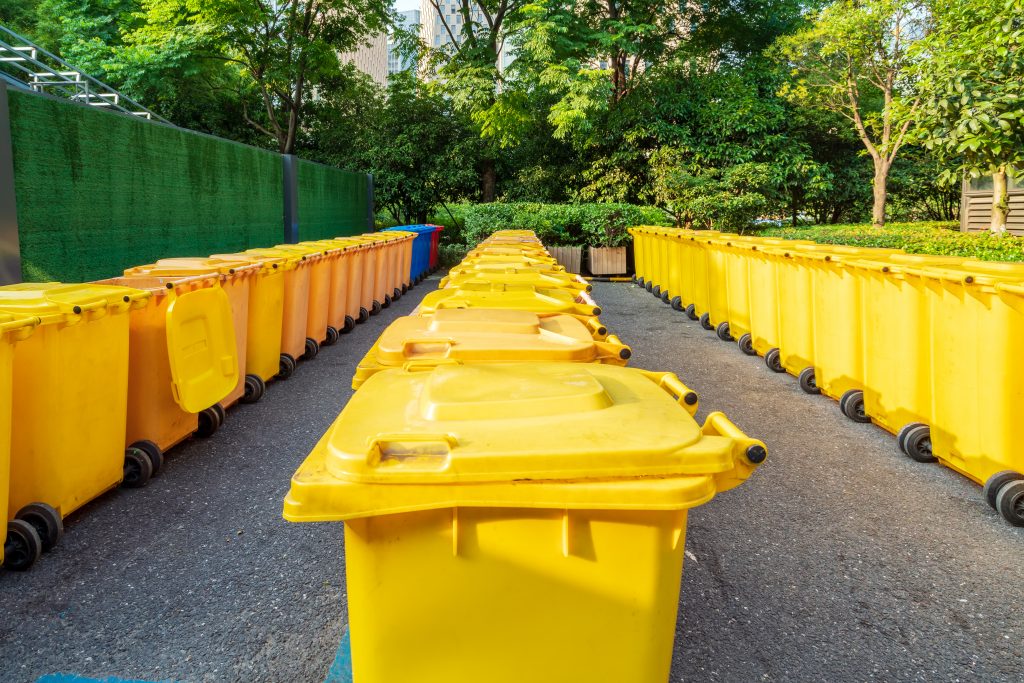
Stay streamlined with Sage warehouse management software
The purpose of having safety inventory is not just for the benefits of your consumers. Though it is high on the priority list, your employees, especially those who manage your warehouses and distribution centres can also take advantage. Sage warehouse management solutions do more than just forecast demands of items. It allows you to have an insight into your warehouse like never before. With minimum and maximum stock level alerts and automatic reordering, your employees know where the stock is, it eliminates the need for your employees to constantly locate and reorder parts, allowing them they will able to stay committed to fulfilling orders to your customers.
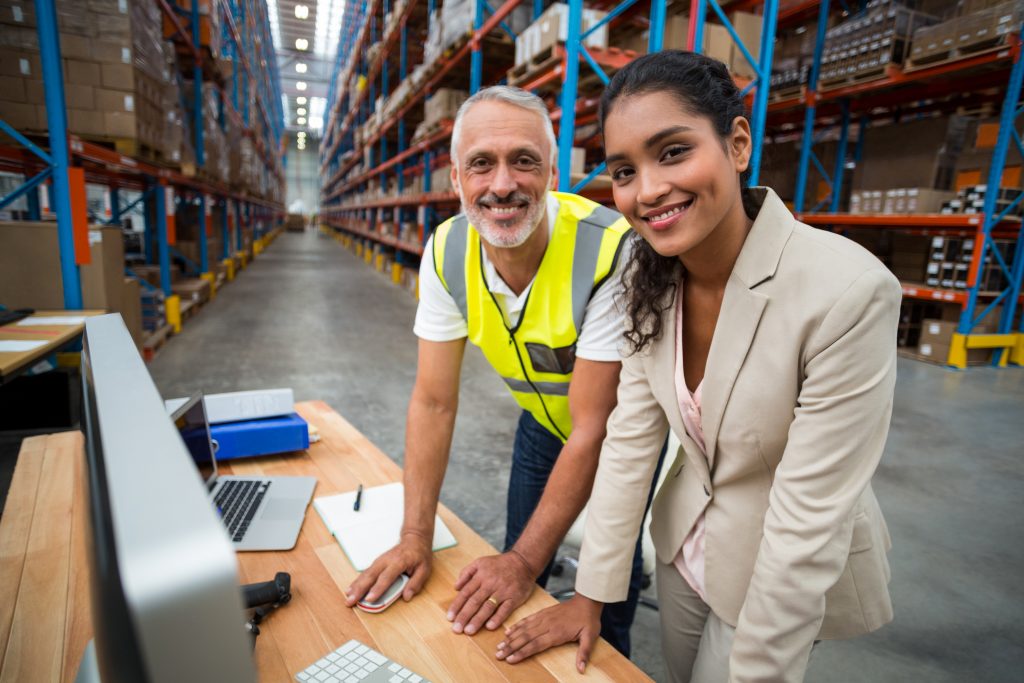
Your customer service levels can go untarnished
The ultimate goal of safety stock? Keeping customers happy. By providing a service where your customer service levels can go untarnished, where your consumers aren’t aware of any changes or disruptions to your processes or supply chains. Perhaps you have a consistent demand for a certain item of inventory which has been highlighted by Sage warehouse management solutions but suddenly you sell more than you forecasted. With safety stock inventory in place, you do not sacrifice your customer service level while you replenish. It also helps your warehouse and supply chain running smoothly as it avoids stock-outs.
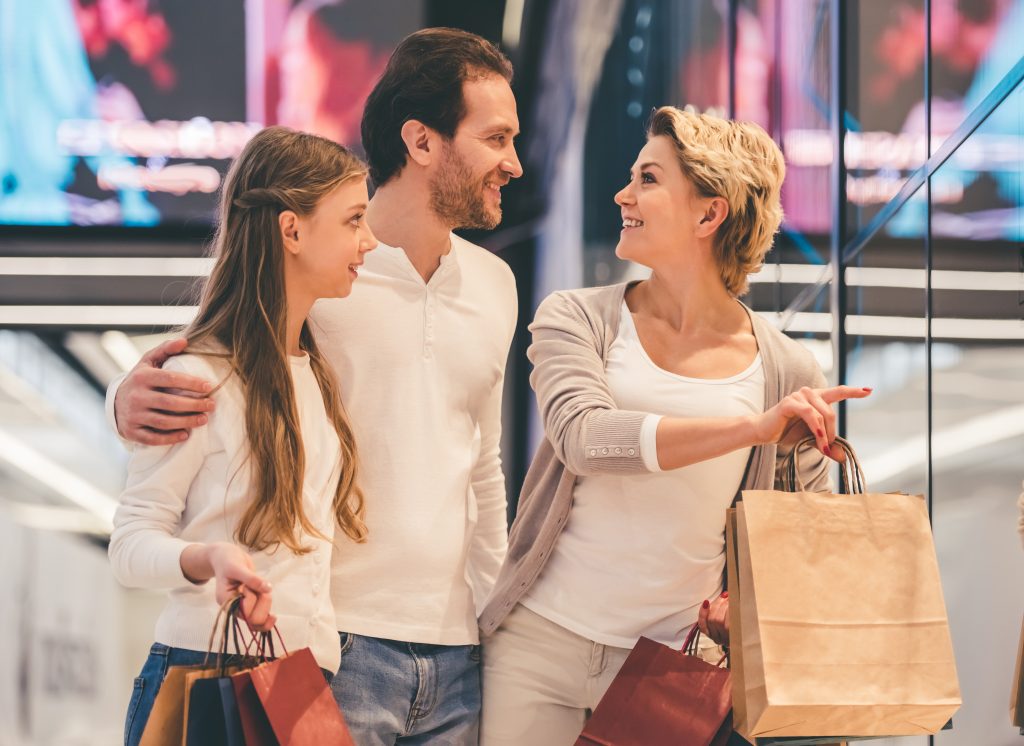
Sage warehouse management solutions help your warehouse to evolve
The best thing you can benefit from when integrating Sage warehouse management solutions is that you are always learning more. This can be anywhere from learning more about your warehouse, learning more about your inventory and learning more about your employees and their processes. Identifying the importance of holding safe stock is just one element to ensure a healthy supply chain and well-organised warehouse. Sage inventory management allows for you to learn about the best practises for calculating stock levels, having accurate data entry and real-time reporting as well being able to forecast supply and demand but not having to do any of it manually.
If you are interested in learning more about how Sage barcoding technology can transform your warehouse or distribution centres, get in touch today.